Vorbereitung für das Verbinden, d.h. Anfasen der Kanten beim Schneiden
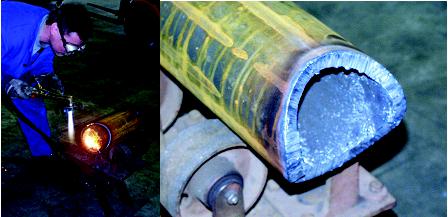
Jeder Schweißer und Produktionstechnologe kennt das Problem, das beim Anschrägen der Kanten von zu schweißenden Teilen auftritt. Das Problem ist umso größer, je größer die Bauteile sind (z. B. im Schiffs- und Brückenbau) oder wenn die Bauteile aus dickeren Materialien bestehen (insbesondere im Bergbau und in der Rüstungsindustrie).
Auch heute noch schneiden die meisten Fabriken Teile senkrecht zum Material und bereiten dann die Schweißphasen vor. Das Verfahren sieht so aus, dass das rechtwinklig geschnittene Stück zu einer Nachbearbeitungsstation transportiert wird, wo es mit einer Fräsmaschine, einem Autogen- oder Plasmabrenner abgeschrägt wird. Oft wird er auch gemahlen. Dadurch verlängert sich der Produktionsprozess, was wiederum zu höheren Kosten führt.
Lösungen, die in letzter Zeit immer beliebter werden, sind 3D-Schneidemaschinen und Roboter, die Materialien in jedem beliebigen Winkel schneiden und anschrägen können. Ihre Anwendung gewährleistet neben einer mindestens 4-fachen Verkürzung des Produktionsprozesses weitere messbare Vorteile:
- Platzersparnis in der Halle - es wird kein sperriges Schrägstativ benötigt, das schädliche Gase, Staub und Lärm emittiert und zusätzlich sicherheitstechnisch geschützt werden muss;
- Geringere Arbeitsintensität und Möglichkeit eines optimaleren Einsatzes der Mitarbeiter;
- kein zusätzlicher Transport von Werkstücken erforderlich;
- höhere Arbeitskultur in der Halle durch den Wegfall der Lärmquelle (Schleifmaschine);
- Verringerung des Brandrisikos durch den Wegfall von manuellen Brennern und Gastanks.
Plasmaschneidanlagen und Autogenschneidanlagen sind aufgrund ihrer geringen Kosten und ihres breiten Anwendungsspektrums am beliebtesten. Der Grund dafür liegt auf der Hand: Baustahl mit einer Dicke von 4 bis 50 mm wird am häufigsten für die Herstellung von Schweißkonstruktionen verwendet. Praktische Versuche mit dem 45°-Fasenschneiden mit einem Plasmaschneider haben gezeigt, dass es bei Materialstärken von 1 bis 35 mm gut funktioniert. Die Brennschneidmaschine hingegen ist bis zu einer Dicke von 200 mm wirksam.
Die Konstruktion einer Maschine zum Anfasen von Blechen stellt für die Hersteller eine große Herausforderung dar. Besonderes Augenmerk muss auf die Positionierung des Schneidkopfes, seine Drehbarkeit und den Ausgleich der Schnittwinkelabweichung gelegt werden.
Die Einhaltung eines konstanten Brennerabstands zum Material ist ebenfalls entscheidend für eine hohe Kantenqualität, insbesondere beim Plasmaschneiden. In der Regel hat das zu schneidende Material keine absolut glatte Oberfläche. Außerdem unterliegt es den Spannungen und vorübergehenden thermischen Einflüssen, die das Plasma beim Schneiden ausübt.
Beim Plasmaschneiden ist das Bezugselement für die Messung des Brennerabstands zum Material die Plasmalichtbogenspannung. Diese Spannung, die im Prinzip leicht zu messen ist, hängt jedoch von vielen Parametern ab. Neben der Höhe des Brenners sind auch der relative Winkel des Brenners, die Stromstärke und die Zusammensetzung des Gasgemischs von Bedeutung. Die Steuerung eines derart komplexen Prozesses erfordert eine computergesteuerte Bewegungssteuerung und eine adaptive Höhenanpassung.
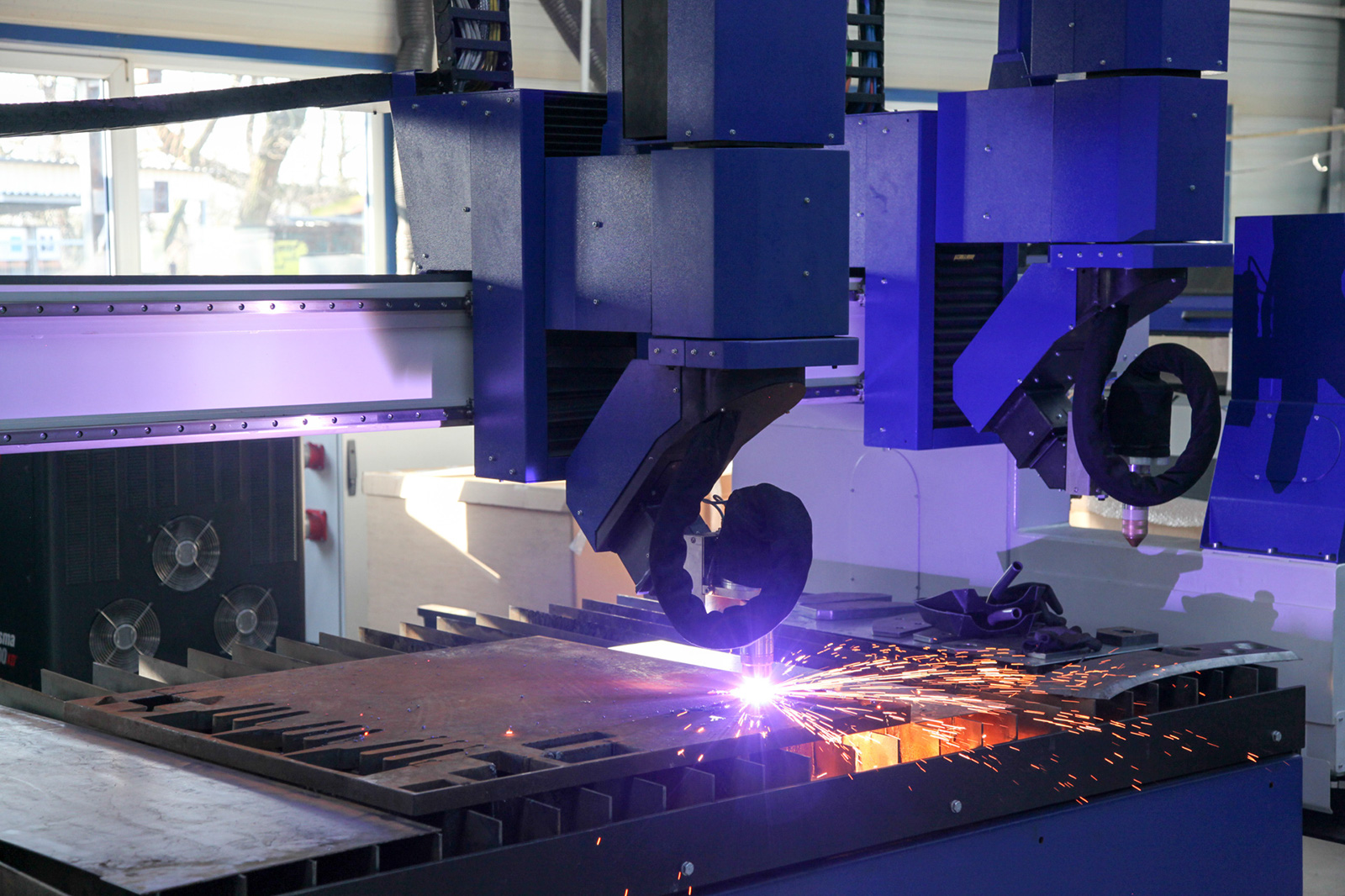
Ein weiterer Vorteil von Fasenanlagen ist die Möglichkeit, Rohre direkt beim Schneiden anzufasen. Ähnlich wie bei den Blechen verkürzt diese Möglichkeit die Vorbereitungszeit erheblich, verbessert die Logistik und senkt die Kosten. Sie ist von großer Bedeutung bei Großprojekten wie dem Bau eines Stadions oder einer Brücke, bei denen oft mehrere tausend Rohre mit Mehrfachanschlüssen verwendet werden.
Für den Entwurf solcher Strukturen wird spezielle CAD-Software verwendet. Es ermittelt selbstständig die benötigte Materialmenge sowie die Art und Anzahl der Verbindungen und reduziert so die Berechnungszeit und Fehler auf ein Minimum.
Während Schneidemaschinen mit festem Schneidkopf bisher die Nase vorn hatten, wächst nun das Interesse an 3D-Schneidemaschinen. Sie bieten sehr messbare Vorteile in Verbindung mit einer Senkung der Kosten und einer Verkürzung der Zeit für die Herstellung eines Elements. Auch Sicherheitsfragen und die Verbesserung der Arbeitshygiene in den Produktionsstätten sind nicht zu vernachlässigen. Die Lösung der Firma Eckert aus Legnica hebt sich von den auf dem Markt erhältlichen Lösungen dieser Art ab. Dabei kommen innovative Technologien zum Einsatz, die eine völlig flexible und effiziente Nutzung der 3D-Schneidefunktionen ermöglichen.